Laboratory for Vibroacoustics
The Chair of Vibroacoustics of Vehicles and Machines possesses a broad variety of measuring devices and analysis software for vibroacoustic applications. You can find a pre-selection of the institute's measurement equipment in the following list:
3D Laser-Scanning-Vibrometer
The Chair possesses a PSV-500-3D Laser-Scanning-Vibrometer from Polytec for the contactless measuring of structural vibrations in a frequency range up to 25 MHz and structural particle velocities from 0,01 µm/s up tp 30 m/s. The 3D system can alternatively be transformed into two independently working 2D Scanning systems. The two one-point-vibrometers PDV-100 are actually parts of the 3D system - however, they can as well be used as independent stand-alone sensors.
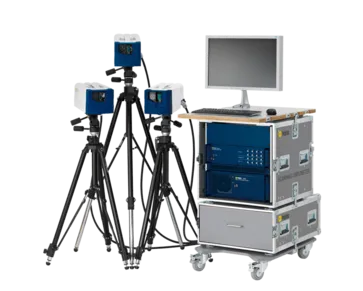
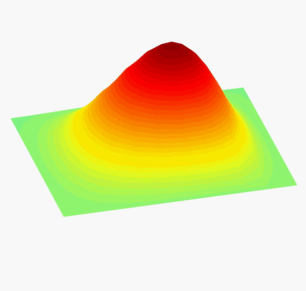
Possible Applications:
- contactless measuring of a three-dimensional structural particle velocity field on surfaces of structures
- unperturbed measuring through fluids (air, water, etc.) possible, e.g. at ultrasonic transducers
- data recording of the strain field caused by a deformation
- measuring of surface waves / Lamb waves for crack identification
- measuring on surfaces of structures with elevated temperature
- sequential scanning of structural vibration forms
System Limitations:
- parallelized measuring of more than three points in case of transient processes
- long-term-measurements of changing operating states
Multichannel Dynamic Signal Analyzer
Raw time data for the analysis of structural dynamic processes (e.g. experimental modal analysis) are generally recorded using a multichannel signal analyzer. The structure is either excited in pulsive manner using an impact hammer or by continuous excitation by use of a shaker. The structural dynamic response is then recorded with accelerometers and a data logger, which records the signals of all accelerometers simultaneously. The Chair possesses the multichannel dynamic signal analyzer "LAN-XI" from Brüel & Kjaer for such measurement types. The system provides 56 input channels as well as multiple options for an automated excitation generation. This system can either be split into multiple, flexible, independent data-logging submodules or it can be used in its full depth for measurements with a high amount input signals (as e.g. for the application of the acoustic camera).

Possible Applications
- general experimental modal analysis using an impact hammer or shaker
- Operational Modal Analysis (OMA - deu: Betriebmodalanalyse)
- operational vibration analysis and order analysis
- long-term measurement of different signals
- third-octave and octave band analysis
- shock analysis of transient processes
- source identification (beamforming / sound intensity measurements)
- psycho-acoustic analyses
System Limitations:
- contactless measurement of light structures
- more than 56 input measurement signals (optional system extension possible)
Additional Measurement Equipment
- impedance tube
- acoustic camera
- microphones, sound intensity sensor
- hand-held sound pressure level measurement device
- accelerometers, laser-based revolution counter
- impact hammers of various sizes
- diverse shakers
- flexible front-ends
Requests for Experimental Observations
Two laboratories - including two vibration-free tables - are provided to the Chair for experimental observations concerning vibroacoustic problems. For queries and further information with respect to measurements or simulations, please do not hesitate to contact us.