Regeneratively produced ammonia as fuel for future marine internal combustion engines in a decarbonized world
Supervisor | Subject |
---|---|
Editor | Cooperation/Funding |
Prof. Dr.-Ing. Thomas Sattelmayer | Ammonia Combustion, Rapid Compression-Expansion Machine, Ignition Process |
Valenitin Scharl, M.Sc., Utkarsh Pathak, M.Sc. | The project is funded by the German Federal Ministry for Economic Affairs and Climate Action on the basis of a decision by the German Bundestag (project no. 03SX534D). The support of the AmmoniaMot consortium (Woodward L’Orange, MAN Energy Solutions, WTZ Roßlau and Neptun Ship Design) is gratefully acknowledged. |
Project
Background
The reduction of greenhouse gas emissions by international shipping marks an important step towards a climate neutral economy. Ammonia (NH3) can serve as a marine fuel and hydrogen H2 carrier, which is more easily transported and stored than liquid H2 The combustion of NH3 in reciprocating engines is challenging due to its high self-ignition temperature, its low flame speed and the propensity to form air pollutants A promising concept for the combustion of NH3 are pilot-ignited dual-fuel engines. However, premixed homogeneous charge combustion with ammonia-air mixtures suffers from considerable ammonia slip and high NOx emissions. The direct injection of main fuel and pilot fuel allows a more flexible control of the combustion process regarding the mixture formation and fuel burnout. Therefore, fuel slip and NOx emissions might be reduced. There has been little research on injection, mixing, ignition and fuel burnout of this concept up until now. In the course of this project, dual-fuel direct injection combustion of ammonia will be investigated experimentally and numerically.
Experimental Studies
Investigations regarding the local mixture formation, ignition and combustion progress are studied in a rapid compression-expansion machine (RCEM). The RCEM is pneumatically driven and the movement of the piston is hydraulically controlled. The absence of a crankshaft allows variable compression ratios. In addition, the temporal and spatial interaction of the main fuel jet and the pilot jet can be varied due to a flexible arrangement of the injectors. This test rig allows full optical access to the combustion chamber via the glass piston.
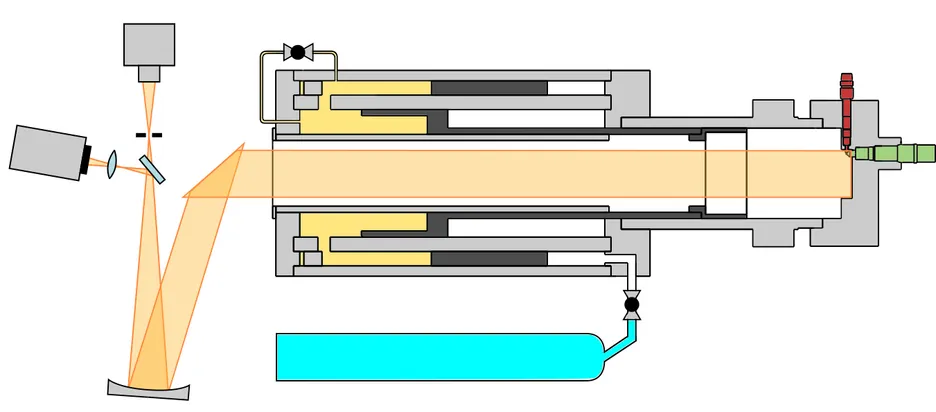
Different measurement techniques will be used to gain information about various combustion quantities. Apart from pressure indication, these include shadowgraphy imaging for spray penetration and structure and OH*-chemiluminescence imaging of the flame propagation. An exhaust gas measurement will be installed to assess the impact of the combustion parameters on air pollutant formation. In addition to combustion experiments, the spray breakup and mixture formation of liquid ammonia sprays are examined in inert atmospheres. The goal of the experimental part is to improve the understanding of the underlying phenomena and to create guidelines for the application of the high pressure dual-fuel combustion in internal combustion engines. In addition, the experimental results will provide a basis for the validation of the numerical model.
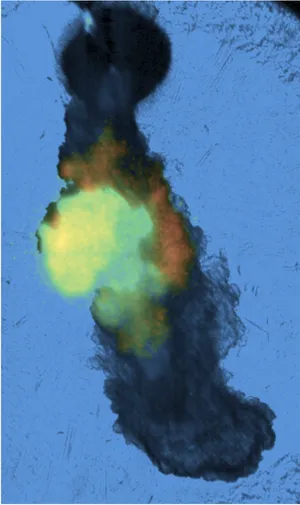
Numerical Investigations
3D-CFD simulations are conducted to gain fundamental insights into the combustion process. The CFD model is based on detailed chemistry in the software CONVERGE. Due to the interaction of two liquid fuel sprays, modeling the direct injection of ammonia and its interaction with the pilot-fuel spray is challenging. The chemical interaction between the two fuels requires a deep understanding of the chemical kinetics. For example, ignition delay times differ from those of pure diesel combustion if diesel and ammonia are mixed. To capture this interaction, in-house reaction mechanisms are created by blending existing mechanisms from literature. After validating the numerical model with the experimental data from the RCEM, the behavior of full engines will be examined. This approach enables a high-quality model validation, while providing valuable insights into real engine characteristics.