Electroforming of rocket combustion chambers
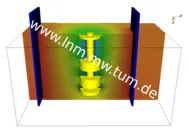

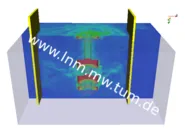
Andreas Ehrl and Volker Gravemeier
In aerospace industry, electroforming techniques enable the efficient realization of components with complex geometry and desired material properties. Within the production process of combustion chambers for space propulsion systems, EADS Astrium uses, among others, an electrodeposition process based on pulsed currents (pulse plating), which allows for generating uniform and relatively thick combustion chamber walls made of nickel.
Numerical simulation enables a new way of investigating and modeling galvanic baths. Computational methods for this purpose have to adequately account for multi-ion transport, fluid mechanics and deposition kinetics in a fully-coupled form.
The project "Numerische Simulation von galvanischen Beschichtungsvorgängen" in cooperation with EADS Astrium was supported by the Raumfahrt-Agentur des Deutschen Zentrums für Luft- und Raumfahrt e.V. in the time period 10/2007- 09/2010. The aim of this project was the development of robust and efficient methods for the coupled numerical simulation of electrochemical deposition processes at industrial scale as well as their application in the context of practical industrial needs.
The project incorporated the mathematical modeling, development and implementation of adequate algorithms, validation of simulation methods, and coupled numerical simulation of electrodeposition processes. A computational method based on multiscale and stabilized finite element methods was developed, with a focus on the coupling of fluid mechanics and electrochemistry. As a result of this project, a comprehensive computational approach for the evaluation of industrial electrodeposition processes was established and is currently further developed.
Publications
Please find publications on this topic here.