Dynamic Behaviour of Hydrogen Flames in Sequential Combustion Systems
Supervisor | Subject |
---|---|
Prof. Dr.-Ing. Thomas Sattelmayer | Thermoacoustic instabilities, Low-frequency, longitudinal modes |
Editor | Cooperation/Funding |
Florian Franke, M.Sc. | This project is funded by the Research Council of Norway, whose support is gratefully acknowledged. |
Motivation and Objectives
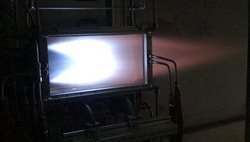
Multi-stage combustion systems are a promising solution for challenges regarding part-load efficiency, turndown ratios, fuel-flexibility and pollutant emissions in power generation gas turbines. Combustion of pure hydrogen is a significant obstacle as state-of-the-art gas turbines are not designed for this unconventional fuel. Hydrogen exhibits a significantly higher reactivity compared to natural gas and other frequently used gas turbine fuels and therefore requires novel combustor designs.
The main goal of this study is the investigation of the dynamic flame response of a hydrogen flame to acoustic perturbations, which is a key input for predictive thermoacoustic stability modelling of gas turbines. The flame response will be identified in the form of flame transfer functions (FTF) and matrices. The FTF provides information on the frequency response of a flame and creates a link between perturbations and the heat release rate response of the flame. Perturbations will be of mixture-reactivity type, fluctuations of the mixture composition and entropy waves.
Experimental Setup
Currently, the Chair of Thermodynamics features the only sequential combustor at laboratory scale available that allows measurements of hydrogen reheat flame dynamics at the required level of thermal power [1]. It features realistic reheat flame conditions as well as ample optical and diagnostic access.
The High-Frequency Transverse Mode Reheat Combustor (HTRC) test rig is modified to also allow the examination of low-frequency longitudinal modes in sequential combustors. The first stage features swirl stabilized combustion with a thermal power of up to 660kW. The fuel for the second stage combustion is injected in the hot exhaust gas stream of the first stage and the reheat flame is stabilized by both propagation and auto-ignition.
Multiple measurement techniques can be applied to investigate flame dynamics, for example the simultaneous measurement of dynamic pressure and OH* and CH* chemiluminescence as well as multi-microphone method for a full identification of the acoustic field. Additionally, the combustor is optically accessible from all lateral sides, allowing for thorough investigation of instability modes.
References
[1] F. Berger et al, A Novel Reheat Combustor Experiment for the Analysis of High- Frequency Flame Dynamics - Concept and Experimental Validation, ASME Turbo Expo 2018, Oslo, Norway 2018.