Combustion Modeling for ALSTOM’s SEV Combustor in LES context
by Rohit Kulkarni, Frédéric Collonval and Wolfgang Polifke
Motivation
Higher power density, reduced emissions and increased efficiency are the major advantages of ALSTOM’s GT 24/GT 26 turbines with sequential combustion.
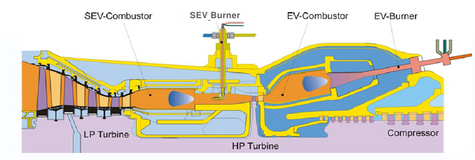
After the main high pressure turbine, about 40% of the fuel is injected into the exhaust gases at about 1000°C in the SEV combustor along with the shielding or carrier air. The shielding air increases the penetration and allows more time for mixture formation. This leads to a multi-stream mixing problem. To design the SEV combustor components, CFD simulations are helpful as they are less costly and less time consuming compared to experimental measurements. This project concentrates on the modeling of turbulence-chemistry interaction in LES context for the SEV combustor.
Objective
The objective of this work is to formulate and implement a computationally efficient turbulence-chemistry interaction model for multi-stream mixing cases involving auto-ignition and flame propagation. The prediction of pollutants like NOx and CO are also in the scope of the project.
Model Approach
The approach used in this work is based on tabulated chemistry. The chemistry is tabulated as a function of two parameters, namely the mixture fraction and the progress variable. This tabulation is done before the 3D CFD simulation in a pre-processing step. The turbulence-chemistry interaction model used is based on the Eulerian transported PDF approach called ’stochastic fields’. This new approach of using tabulated chemistry with stochastic fields method is computationally less expensive as fewer transport equations need to be solved in LES compared to detailed chemistry. This method bypasses the problem of the PDF shape and modeling of the higher moments occurring in presumed PDF approaches. This makes the model suitable for multi-stream mixing cases.
Validation
The model has been validated for two auto-ignition experiments.
Case 1: The first case, known as Markides experiment [1], is a binary (2 stream) case, in which a jet of diluted hydrogen is injected into an electrically heated co-flow of hot air. The autoignition length depends on the temperature of the co-flow. The auto-ignition length predicted by the model is compared with the experimental measurements for different co-flow temperatures in Fig.2.
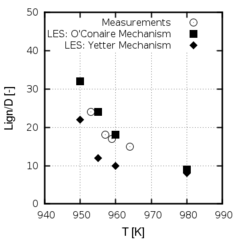
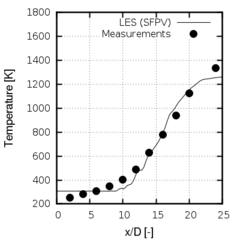
The difference in the results using the two different mechanisms shows the importance of the chemical mechanism used for the tabulation.
Case 2: The second validation case is a lifted jet flame called ’Cabra flame’ [2]. In this case a jet of dilute hydrogen is injected into a co-flow of hot combustion gases (1045 K). The experimental flame lift-off height was reported to be 45 mm (10D). Fig. 3 shows the comparison between the measured and simulated time averaged temperature along the axis of the jet.
Fig.4 shows a snapshot of the temperature contour from the LES. The validation of the model for the SEV combustor is currently in progress.
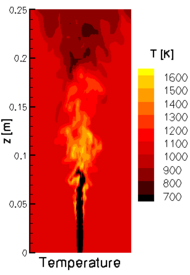
References
[1] C. N. Markides et. al., Experimental study of hydrogen autoignition in a turbulent co- flow of heated air. Proceedings of the Combustion Institute, 883-891, 2005
[2] R. Cabra, et.al., Berkeley Jet Flames in a Vitiated Coflow. Proc. Combust. Inst, 29:1881-1888, 2002